Cooling Tower Filtration
Many industries use cooling towers to cool down process and utility streams. A cooling tower circulates water via heat exchangers, some of the water continuously evaporates and some is blown down when water salinity reaches a high level. Make-up water is inserted to compensate the loss. Chemicals such as biocides, corrosion inhibitors and anti scalants are constantly added to reduce corrosion, biofouling and scaling potential. Most of the time, a mechanical /media filtration system is added to filter around a 10% side-stream to prevent solids accumulation.
The problem
Total consumption of chemicals can be very high and consequently running costs are high. Also, some of the chemicals, especially the biocides may not be effective. Side stream filtration is normally non-effective for two main reasons:- Degree of the mechanical filtration is too low to be effective
- A combination of mineral deposition and biofouling lowers the performance of quartz based media filters
Dryden Aqua process solution
- Adding AFM® Activated Filter Media filtration on a side stream of approx. 10%
- AFM® is a bio resistant media with high surface oxidation potential resulting in dramatically reduced biofouling potential and biocides concentration
- Due to AFM®'s hydrophilic properties, there is no scaling development on the AFM surface guaranteeing high and continuous filtration performance
- As a result of its high surface area and high filtration capacity, AFM® media is effectively cleaning the cooling tower environment even with high concentration cycles
- Total running costs (mainly biocides) are dramatically reduced
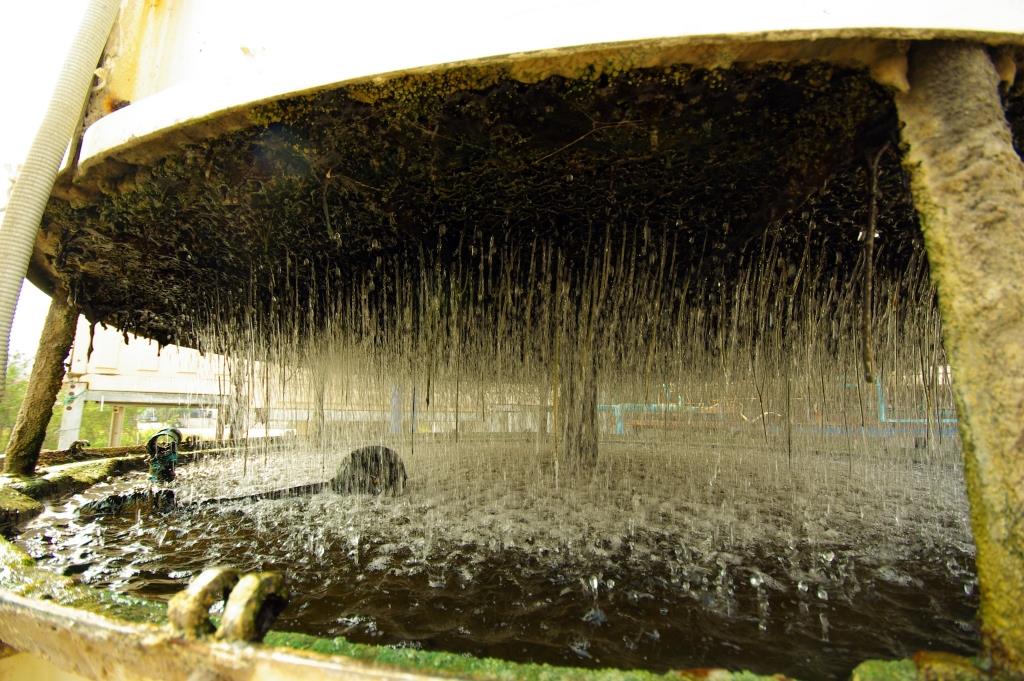
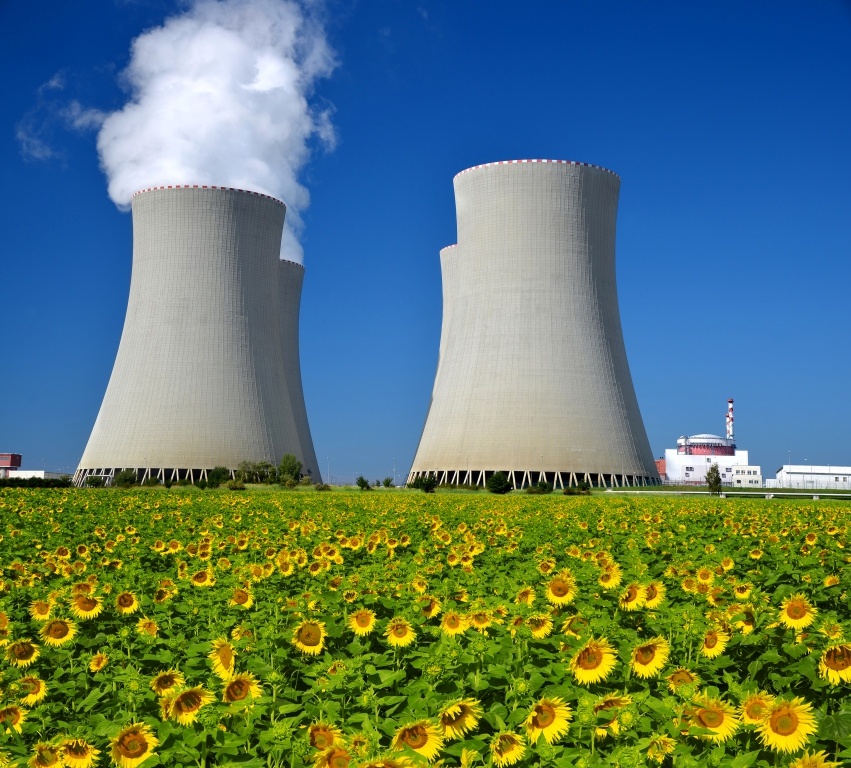
Technical solution summary
PARAMETER |
|
---|---|
Side stream filtration percentage |
10% |
Filtration velocity range (m3/hr/m2) |
15-20 |
AFM® grades required (from bottom to top on a lateral) |
30 cm grade 3 20 cm grade 2 40-90 cm grade 1 |
AFM® Back wash velocity range (m3/hr/m2) |
45 - 50 |
Expected Degree of filtration |
5-10 microns |
AFM® expected lifetime range |
10-20 years |